sensores próximos
Sensores de pressão
O que é um sensor de pressão para água?
A pressão é definida como a força por unidade de área que um material sólido, líquido ou gasoso exerce sobre uma superfície. A unidade reguladora do S.I. para pressão é o Pascal (N/m2), mas na prática são usadas outras unidades como bar, atmosfera, milímetros de mercúrio ou psi (libras por polegada quadrada).
Os sensores de pressão para água normalmente são transdutores, ou seja, transformam a pressão medida pelo elemento sensor em uma saída analógica elétrica normalizada e padrão. Principalmente encontraremos sensores com saída de 4-20 mA ou 0-10 V, embora ultimamente devido aos requisitos de adaptação para nós IoT outras saídas elétricas estejam sendo usadas: 1-5 V, 0-5 V, 0,5-4,5 V e saída RS-485 com ModBus. O sinal elétrico fornecido é análogo ao valor da pressão medida, menos o valor que nos é dado pelas comunicações, os transmissores, que nos dão diretamente a pressão na unidade escolhida.
; Portanto, no mercado podemos encontrar uma infinidade de variantes.
São essenciais tanto para a gestão da rega como para a sua gestão energética e devem ser devidamente distribuídos na rede de rega para monitorização
-
-
- Monitoramento da pressão na rede de distribuição, é a aplicação mais simples e permite saber como está se desenvolvendo o processo de distribuição e impulsão da água.
- Reduzindo o consumo de energia: Medindo a pressão em pontos críticos do sistema, podemos ajustar a velocidade ideal das bombas. logicamente teremos que ter controle sobre estes através de variadores de velocidade. É o que se chama de gerenciamento de pressão e tenta reduzir pressões excessivas ou desnecessárias, tornando o sistema mais eficiente. Trata-se de encontrar os níveis ideais de serviço.
- Melhorar a qualidade da irrigação: se a pressão for monitorada na parcela, será possível obter a melhor uniformidade de irrigação possível controlando sua pressão.
- Estudo de eficiência na distribuição de água: Com vários sensores podemos determinar as perdas de carga que ocorrem em elementos singulares de distribuição de água (caldeiras, filtros, etc.) e em seções da mesma . Com a coleta desses dados e sua análise, é possível prever possíveis falhas futuras e buscar soluções e remédios antes que elas ocorram, minimizando as perdas de água.
- Estudo da eficiência das bombas: Se o desempenho do sistema de bombeamento for monitorado e os registros históricos estiverem disponíveis, podem ser estabelecidos limites mínimos de eficiência para que, se a eficiência cair abaixo desses valores, alarmes são gerados e medidas corretivas podem ser tomadas.
Você pode medir indiretamente o nível de água em um tanque (sensores de pressão hidrostática) e também o fluxo circulante através de um tubo (medidores de vazão de pressão diferencial).
-
As quatro tecnologias mais importantes para medição de pressão são: medição com sensores resistivos, sensores piezoresistivos, sensores capacitivos e sensores piezoelétricos. Vamos ver o funcionamento dos sensores de pressão com base nesses princípios.
-
-
- Sensores de pressão resistiva usam medidores de tensão que são resistência variável com deformação e deformação induzida por pressão. Para isso, utiliza-se uma membrana sobre uma chapa metálica de espessura reduzida para poder flexionar de forma controlada em função da pressão, e sobre a membrana são colocados extensômetros, cuja variação ôhmica é medida por meio de uma ponte de Wheatstone que fornece resultados precisos e estáveis. A deformação de uma membrana é transformada em um sinal elétrico. Devido à rigidez de sua construção, são utilizados para medir altas pressões.
-
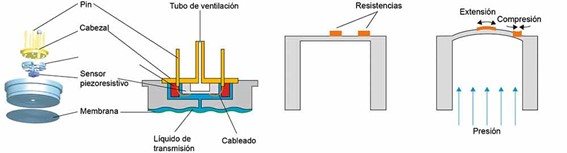
← Fig: Diagrama de um sensor de pressão resistiva. Uma resistência variável com deformação (strain gauge) é colocada sobre uma membrana e esta é colocada sobre uma fina chapa metálica que se deforma em função da pressão a que é submetida por uma das faces da sua superfície. O valor da pressão na chapa será obtido a partir do valor ôhmico do extensômetro.
-
-
- Os sensores de pressão com tecnologia capacitiva são baseados na medição da capacitância de um capacitor variável em função da pressão. Para isso, utiliza-se como dielétrico uma membrana com duas placas metálicas que a envolvem, que constituem o capacitor. A deformação da membrana, induzida pela pressão, reduz a distância entre as duas placas, aumentando a capacidade e mantendo a área superficial e a constante dielétrica. Essa mudança na capacidade pode ser medida eletricamente e correlacionada com a pressão aplicada.
Esses tipos de sensores são limitados a baixas pressões, até cerca de 40 bar, e permitem a medição de pressão com alta sensibilidade. Como a membrana permite a deformação máxima até que se apoie na placa estática, eles têm um alto grau de segurança contra sobrecarga. As limitações práticas são determinadas pelo material e características da membrana e pelas técnicas de união e vedação.
- Os sensores de pressão com tecnologia capacitiva são baseados na medição da capacitância de um capacitor variável em função da pressão. Para isso, utiliza-se como dielétrico uma membrana com duas placas metálicas que a envolvem, que constituem o capacitor. A deformação da membrana, induzida pela pressão, reduz a distância entre as duas placas, aumentando a capacidade e mantendo a área superficial e a constante dielétrica. Essa mudança na capacidade pode ser medida eletricamente e correlacionada com a pressão aplicada.
-
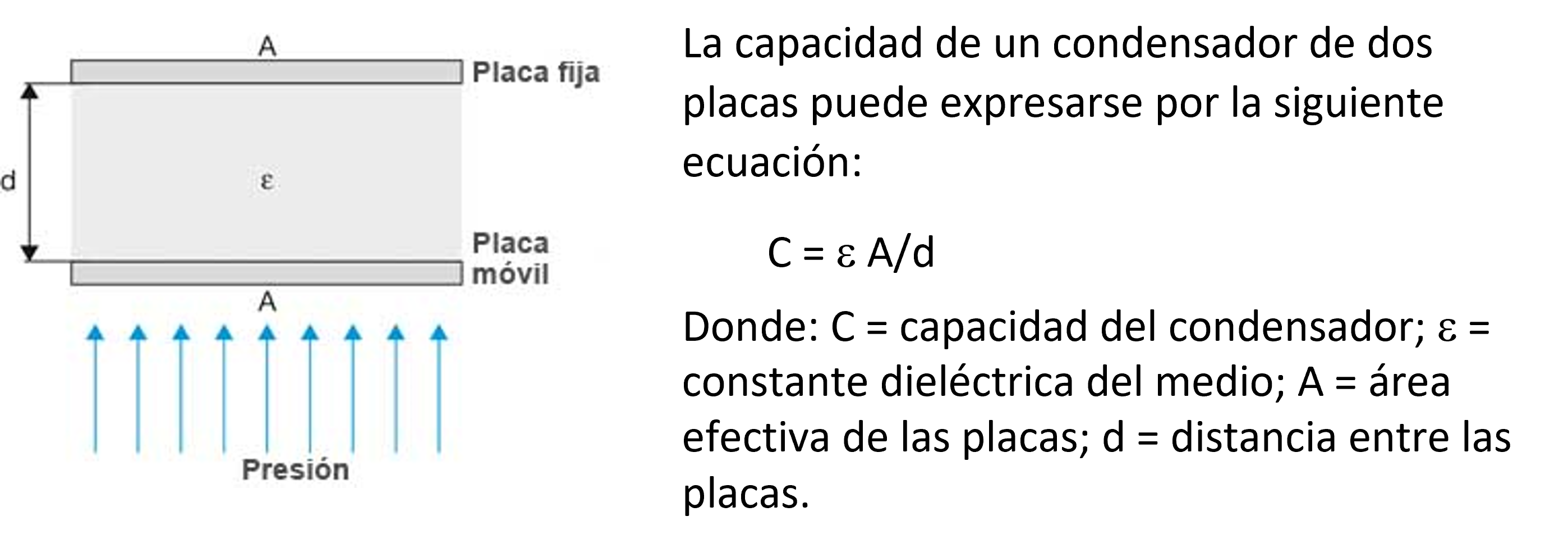
← Fig: Esquema teórico do funcionamento de um sensor de pressão capacitivo. Se a distância entre as placas que compõem o capacitor for encurtada devido à pressão que queremos medir, a capacidade desse capacitor muda. Esta capacidade pode ser medida diretamente e a partir daqui obter a pressão na placa móvel
-
-
- Sensores de pressão piezoelétricos: é baseado em um efeito físico que ocorre em alguns cristais não condutores, como o quartzo. Quando o quartzo é comprimido, uma polarização elétrica proporcional à pressão é produzida. A tensão elétrica gerada pela carga na superfície do cristal pode ser captada e amplificada. Sua desvantagem é que só é capaz de medir variações de pressão, mas se a pressão for estática o sensor não é capaz de medi-la.
-
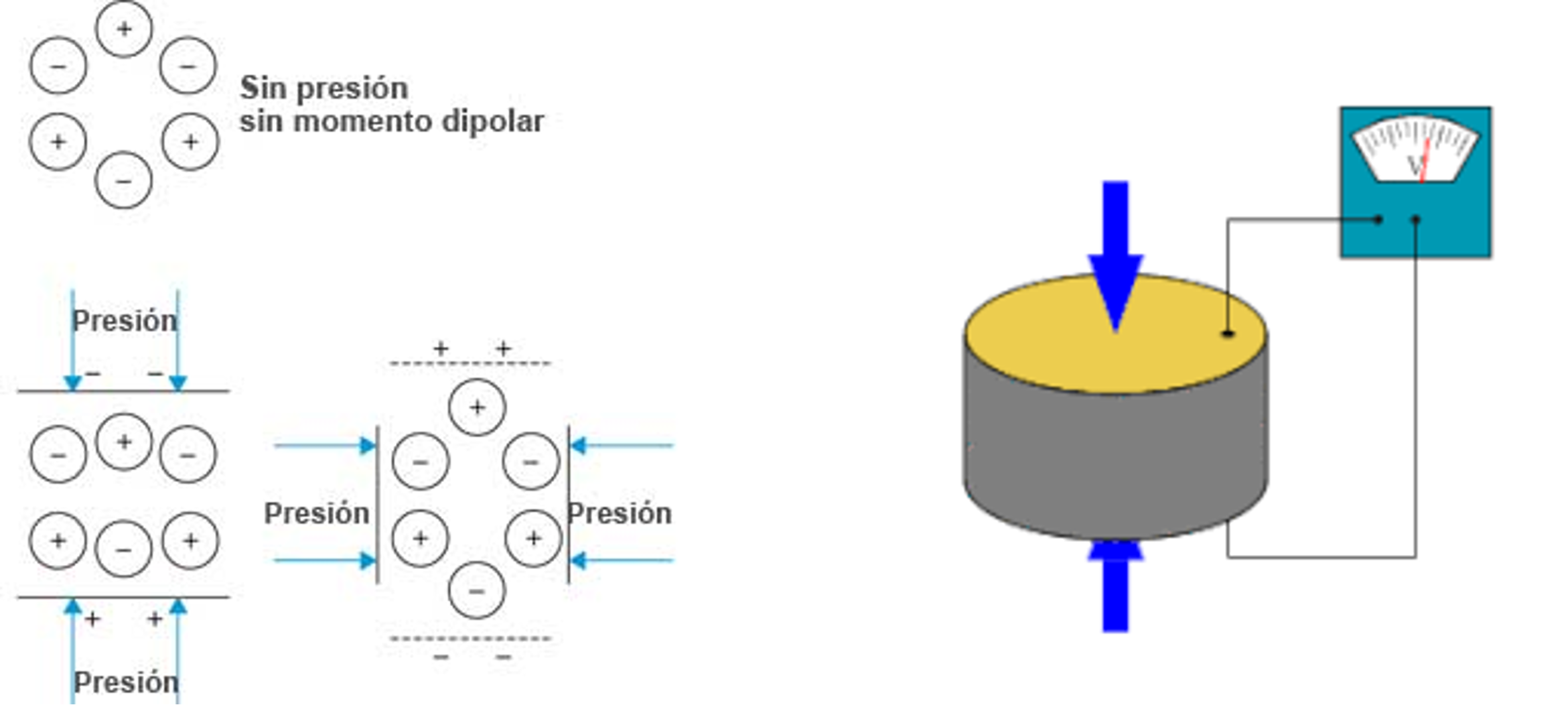
← Fig: Esquema teórico del funcionamiento de un sensor de presión piezoeléctrico. Al someter a un cristal piezoeléctrico (por ejemplo, cuarzo) a la acción mecánica de la compresión, las cargas del cristal se separan. Esto propicia una polarización de la carga existente (un flujo de electrones se dirige hacia un extremo y genera en él una carga negativa, mientras que en el extremo opuesto se induce una carga positiva). La corriente que puede generar es proporcional al área de la placa y a la rapidez de la variación de la presión aplicada ortogonalmente a la superficie de la placa
-
-
- Os sensores de pressão piezoresistivos consistem em uma membrana (principalmente de silício) com extensômetros integrados feitos de semicondutores que detectam a deformação devido à pressão aplicada. Esses extensômetros geralmente são configurados como uma ponte de Wheatstone para reduzir a sensibilidade e aumentar a potência de saída. Essa ponte com semicondutores é um fator de 10 a 100 vezes maior do que com resistores de metal puro. Devido ao material utilizado, podem ser utilizados até pressões em torno de 1000 bar.
Strain gauges metálicos montados em ponte de Wheatstone podem ser colocados em qualquer material, enquanto os feitos com semicondutores são incorporados como uma microestrutura na membrana, portanto a deformação é feita diretamente, mas eles têm a desvantagem de serem muito sensíveis à temperatura e exigirem uma compensação individual para cada sensor.
- Os sensores de pressão piezoresistivos consistem em uma membrana (principalmente de silício) com extensômetros integrados feitos de semicondutores que detectam a deformação devido à pressão aplicada. Esses extensômetros geralmente são configurados como uma ponte de Wheatstone para reduzir a sensibilidade e aumentar a potência de saída. Essa ponte com semicondutores é um fator de 10 a 100 vezes maior do que com resistores de metal puro. Devido ao material utilizado, podem ser utilizados até pressões em torno de 1000 bar.
-
Tipos de medições de pressão
Para escolher um sensor de pressão, é essencial entender que são considerados 3 tipos de pressão, correspondentes a diferentes modalidades de sensor.
Como mencionado, a maioria das tecnologias de sensores de pressão medem a deformação de uma membrana sob o efeito da pressão exercida sobre ela, sendo este o valor que você deseja saber. Como a membrana tem dois lados, outra pressão é aplicada no segundo lado, então a deformação medida é o resultado da diferença de pressão entre os dois lados da membrana.
São considerados 3 tipos de pressão de referência (absoluta, relativa e diferencial) e, portanto, teremos 3 tipos de sensores:
-
-
- Sensores de pressão absoluta medem a pressão em relação a uma câmara de referência sob vácuo (próximo ao vácuo). A deformação da membrana corresponde exatamente à pressão medida. Tem a vantagem de não serem afetados pelas mudanças na pressão atmosférica e, além disso, as mudanças na temperatura influenciam menos o seu funcionamento.
- Sensores de pressão relativa (manômetros ou manômetros) são usados para medir a pressão em relação à pressão atmosférica atual. O segundo lado da membrana é submetido à pressão atmosférica. Sua deformação é igual à diferença entre a pressão medida e a pressão ambiente.
- Sensores de pressão relativa padronizados (manômetros selados ou de referência constante) são como sensores de pressão relativa que medem pressão em relação a uma pressão fixa, em vez de em relação a a pressão atmosférica existente.
Sensores de pressão diferencial determinam a diferença entre duas pressões e podem ser usados para medir quedas de pressão, níveis de fluido e vazões. Tecnicamente, a maioria dos sensores de pressão são, na verdade, sensores de pressão diferencial. Por exemplo, um manômetro é um sensor de pressão diferencial com uma extremidade aberta para a pressão ambiente.
-
Quando a pressão medida por um sensor de pressão relativa ou manômetro é igual à da atmosfera, a pressão manométrica é igual a zero, portanto não há diferença de pressão entre os sistemas analisados e o ambiente atmosférico. Quando um manômetro é conectado ao sistema cuja pressão se deseja medir, ele mede o excesso de pressão em relação à pressão atmosférica. Se a pressão no referido invólucro for menor ou igual à atmosférica, indica zero.
Um vácuo perfeito corresponderia a zero pressão absoluta. Todos os valores de pressão absoluta são positivos.
Pressões abaixo da atmosférica são chamadas de pressões de vácuo. Quando o sensor de pressão mede pressões abaixo da atmosférica, ele é chamado de sensor de pressão a vácuo ou vacuômetro.
Pman = Pabs – Patm (para pressões maiores que Patm )
Pvac = Patm – Pabs (para pressões menores que Patm )
onde Pman = pressão manométrica; Pvac = Pressão de vácuo; Pabs = pressão absoluta; Patm = Pressão atmosférica.
Fig: Esquema de relaciones entre la presión absoluta, atmosférica y manométrica →
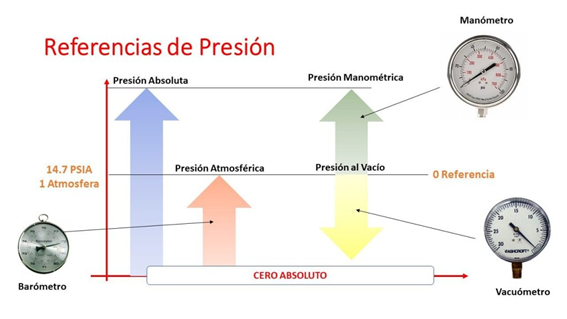
Variáveis físicas medidas indiretamente com pressão
Existem variáveis como nível e fluxo que podem ser medidas por meio de sensores de pressão.
-
-
- Medição de nível com sensores de pressão: sensores de pressão hidrostática.
- Sensores de pressão diferencial: medição de vazão.
-
Como escolher um sensor de pressão
Depois de saber se você precisa medir pressão absoluta, relativa ou diferencial e ter escolhido uma tecnologia de sensor, você terá que escolher o modelo correto de acordo com os seguintes critérios:
Recursos estáticos:
-
-
- Antes de tudo, é importante escolher um sensor cuja faixa de medição corresponda à faixa de pressão a ser medida, levando em consideração as condições normais e possíveis variações de pressão.
- É claro que não devemos esquecer as especificações das características de medição que precisamos para nossa aplicação, como na escolha de qualquer sensor: Precisão, Repetibilidade, histerese, desvio< /strong>, etc.
-
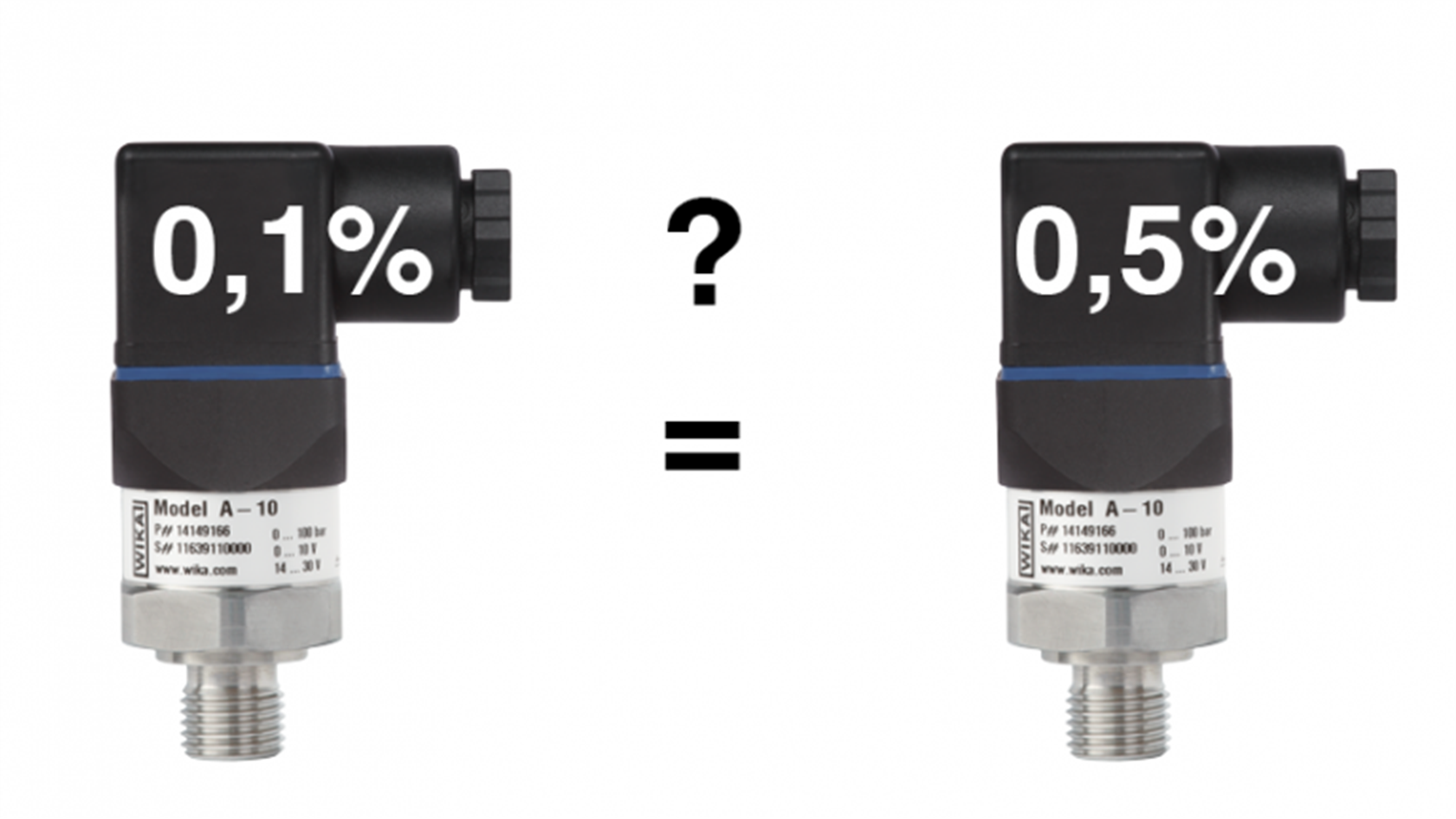
← Fig: A precisão e o baixo drift do sensor influenciam no seu preço. Quanto mais preciso, mais caro. O desvio pode ser corrigido calibrando o sensor uma vez por ano. A histerese é o único parâmetro que não poderemos corrigir
Recursos ambientais:
-
-
- A temperatura operacional em nossas aplicações não desempenha um papel significativo. A maioria dos sensores tem uma faixa operacional de -25°C a 100°C.
- Características mecânicas: Grau de proteção IP. Grau de proteção EX. Grau de proteção IK.
-

Características elétricas:
-
-
- Tensão de alimentação: 5 Vdc, 10-30 Vdc , etc.
- Sinal de saída: Como qualquer outro sensor, você deve escolher um sensor de pressão cujo sinal de saída possa ser captado por nosso equipamento eletrônico: 4-20 mA; 0-10 V; 0-5V; etc Também podemos encontrar sensores com saídas de comunicação industriais (Modbus sobre RS-485) ou eletrônicas (I2C, SPI)
- Consumo (Se vai ser alimentado por um nó autónomo, é um dos parâmetros que o sensor a instalar irá definir).
- Proteções contra surtos e curtos-circuitos.
- Conexão elétrica: 2/3/4 fio, tipo conector. Vamos encontrar vários tipos de saída, mas devemos sempre escolher uma padronizada para facilitar a troca em caso de quebra.
-
- Conexão de processo: O último critério-chave a ser escolhido é a configuração do sensor e como ele é montado no ponto de medição. A maioria dos sensores são rosqueados com roscas padrão, o que permite que sejam facilmente montados em um bocal instalado em tubulações, tanques, etc. Existem também sensores equipados com flanges.
Como podemos ver, existem muitas variantes a especificar para garantir uma adaptação ideal à nossa aplicação, por isso é interessante escolher marcas que tenham um amplo catálogo com padronização conexões e que especificam bem as características dos sensores.