sensores cercanos
Sensores de Presión
¿Qué es un sensor de presión para agua?
La presión se define como la fuerza por unidad de área que un material sólido, liquido o gaseoso ejerce sobre una superficie. La unidad reglamentaria por el S.I. para la presión es el Pascal (N/m2), pero en la práctica se utilizan otras unidades como el bar, la atmosfera, milímetros de mercurio o el psi (libras por pulgada cuadrada).
Los sensores de presión para agua normalmente son transductores, es decir transforman la presión medida por el elemento sensor en una salida análoga eléctrica normalizada y estándar. Principalmente nos encontraremos sensores con salida 4-20 mA ó 0-10 V, aunque últimamente debido a los requerimientos de adaptación para los nodos IoT se están utilizando otras salidas eléctricas: 1-5 V, 0-5 V, 0,5-4,5 V y salida RS-485 con ModBus. La señal eléctrica proporcionada es análoga al valor de presión medido, menos lo que nos dan el valor por comunicaciones, los transmisores, que nos dan directamente la presión en la unidad elegida.
Los rangos de presión de medida son muy amplios, lo mismo ocurre con las características del sensor como las conexiones eléctricas, conexiones a procesos, tipo de salida eléctrica, tipo de medida, etc; Por lo que en el mercado nos podremos encontrar con multitud de variantes.
Son fundamentales tanto para la gestión del riego como para la gestión energética de estos y se deben distribuir adecuadamente en la red de riego para su monitorización
Aplicaciones en el campo del agua
-
-
- Monitorización de la presión en la red de distribución, es la aplicación más simple y nos da a conocer cómo se está desarrollando el proceso de la distribución e impulsión de agua.
- Reducción del consumo energético: Con la medición de la presión en puntos críticos del sistema podremos ajustar el punto óptimo de velocidad de las bombas. lógicamente tendremos que tener un control sobre estas mediante variadores de velocidad. Esto es lo que se llama gestión de la presión y trata de reducir las presiones excesivas o innecesarias, haciendo que el sistema sea más eficiente. Se trata de buscar los niveles óptimos del servicio.
- Mejorar la calidad del riego: si se monitoriza la presión en parcela se podrá obtener la mejor uniformidad en el riego posible al controlar la presión de este.
- Estudio de la eficiencia en la distribución de agua: Con varios sensores podemos determinar las Pérdidas de presión que se producen en elementos singulares de la distribución de agua (calderines, filtros, etc) y en tramos de esta. Con la recopilación de estos datos y su análisis, se puede, prever posibles fallos futuros y buscar soluciones y remedios antes de que esto ocurra, minimizar las pérdidas de agua.
- Estudio de la eficiencia de las bombas: Si se monitoriza el rendimiento del sistema de bombeo y se tienen históricos, se puede establecer unos umbrales de eficiencia mínima de forma que si la eficiencia baja por debajo estos valores se generen alarmas y se puedan tomar medidas correctivas.
Indirectamente se puede medir el nivel de agua en un depósito (sensores de presión hidrostáticos) y también el caudal circulante por una tubería (Medidores de Flujo por presión Diferencial).
-
Principios de funcionamiento de los sensores de presión
Las cuatro tecnologías más importantes de medir la presión son: medida con sensores resistivos, sensores piezoresistivos, sensores capacitivos y sensores piezoeléctricos. Veamos el funcionamiento de los sensores de presión basados en estos principios.
-
-
- Los sensores de presión resistivos utilizan galgas extensométricas que son resistencias variables con la deformación y esta es inducida por la presión. Para ello se utiliza una membrana sobre una lámina metálica que tiene un grosor reducido para poder flexar de manera controlada en función de la presión, y sobre la membrana se sitúan las galgas extensiométricas, cuya variación óhmica es medida usando un puente de Wheatstone que proporciona resultados precisos y estables. Se transforma la deformación de una membrana en una señal eléctrica. Debido a la rigidez de su construcción, se utilizan para medir presiones elevadas.
-
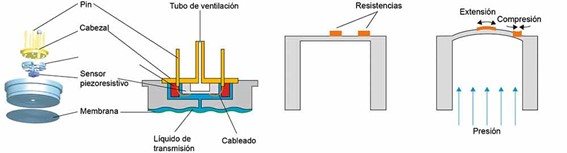
← Fig: Esquema de un sensor de presión resistivo. Sobre una membrana se coloca una resistencia variable con la deformación (galga extensiométrica) y esta se coloca sobre una lámina metálica delgada que se deforma en función de la presión a la que es sometida por una cara de su superficie. El valor de la presión sobre la lámina metálica se obtendrá a partir del valor óhmico de la galga extensiométrica.
-
-
- Los sensores de presión con tecnología capacitiva están basados en la medición de la capacidad de un condensador variable en función de la presión. Para ello se utiliza una membrana como dieléctrico con dos placas metálicas que la rodean que constituyen el condensador. La deformación de la membrana, inducida por la presión, reduce la distancia entre las dos placas, aumentando la capacidad y manteniendo igual la superficie y la constante dieléctrica. Este cambio en la capacidad se puede medir eléctricamente y correlacionarse con la presión aplicada.
Este tipo de sensores están limitados a presiones bajas, hasta alrededor de 40 bar y permite la medición de presión con elevada sensibilidad. Dado que la membrana permite una deformación máxima hasta apoyarse en la placa estática tienen una elevada seguridad contra sobrecarga. Las limitaciones practicas están determinadas por el material y las características de la membrana y las técnicas de unión y sellado.
- Los sensores de presión con tecnología capacitiva están basados en la medición de la capacidad de un condensador variable en función de la presión. Para ello se utiliza una membrana como dieléctrico con dos placas metálicas que la rodean que constituyen el condensador. La deformación de la membrana, inducida por la presión, reduce la distancia entre las dos placas, aumentando la capacidad y manteniendo igual la superficie y la constante dieléctrica. Este cambio en la capacidad se puede medir eléctricamente y correlacionarse con la presión aplicada.
-
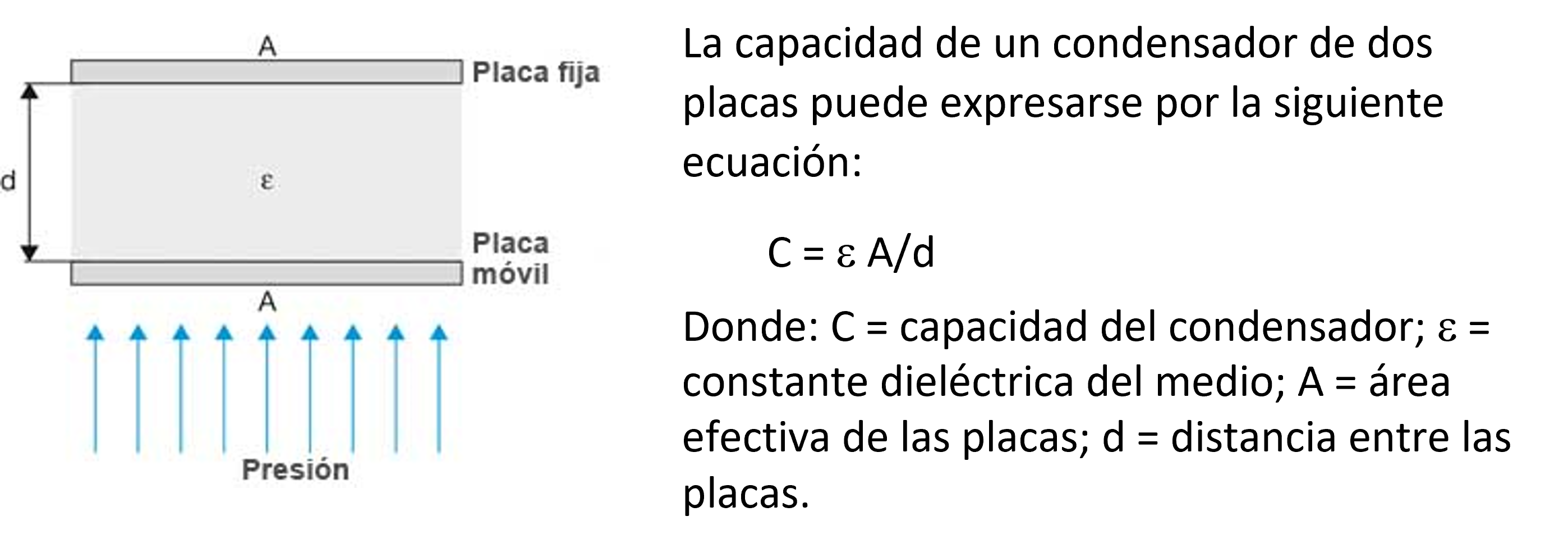
← Fig: Esquema teórico del funcionamiento de un sensor de presión capacitivo. Si la distancia entre las placas que forman el condensador se acorta debido a la presión que queremos medir, la capacidad de este condensador cambia. Esta capacidad se puede medir directamente y a partir de aquí obtener la presión sobre la placa móvil
-
-
- Sensores de presión piezoeléctricos: se basa en un efecto físico que sucede en unos pocos cristales no conductivos como el cuarzo. Cuando se comprime el cuarzo se produce una polarización eléctrica proporcional a la presión. La tensión eléctrica generada por la carga en la superficie del cristal puede captarse y amplificarse. Su desventaja es que solo es capaz de medir las variaciones de presión, pero si la presión es estática el sensor no es capaz de medirla.
-
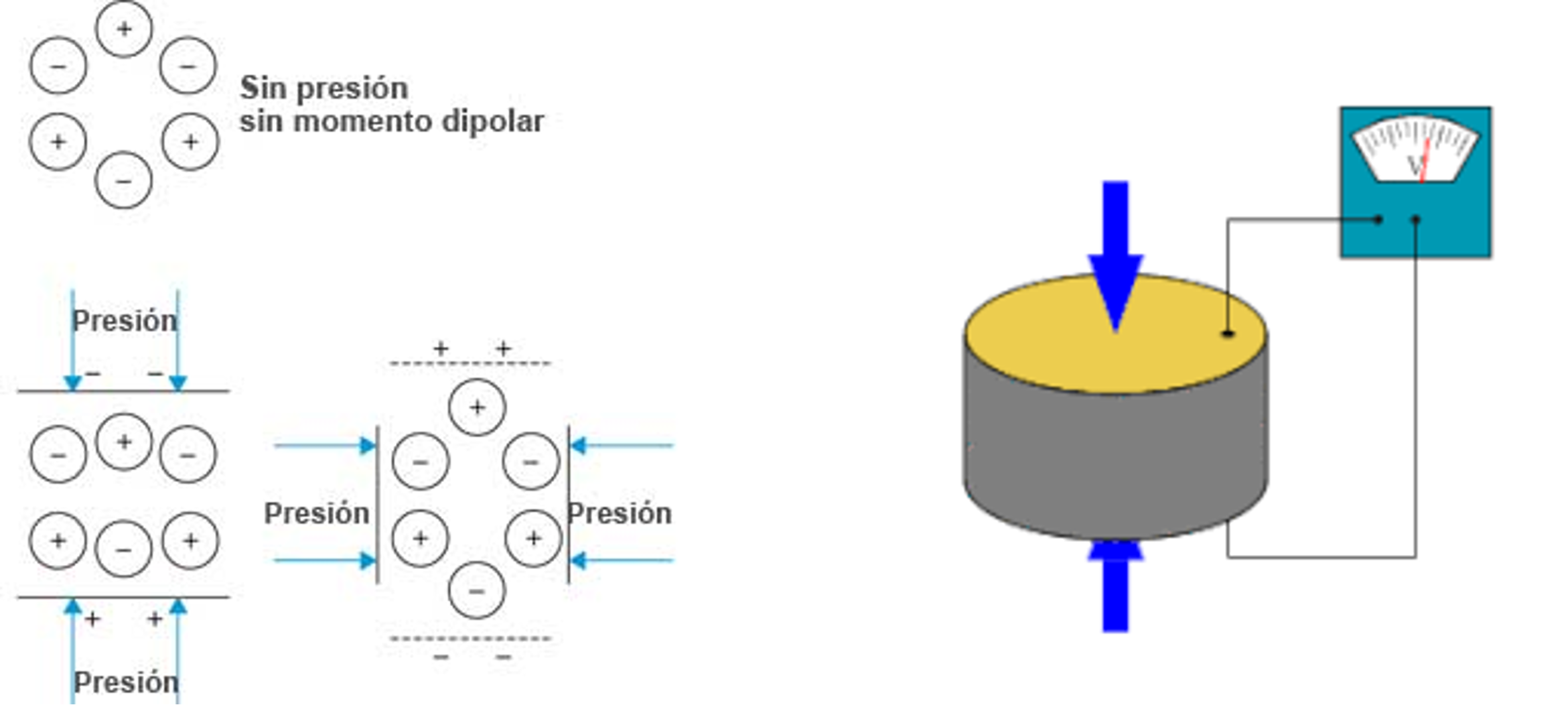
← Fig: Esquema teórico del funcionamiento de un sensor de presión piezoeléctrico. Al someter a un cristal piezoeléctrico (por ejemplo, cuarzo) a la acción mecánica de la compresión, las cargas del cristal se separan. Esto propicia una polarización de la carga existente (un flujo de electrones se dirige hacia un extremo y genera en él una carga negativa, mientras que en el extremo opuesto se induce una carga positiva). La corriente que puede generar es proporcional al área de la placa y a la rapidez de la variación de la presión aplicada ortogonalmente a la superficie de la placa
-
-
- Los sensores de presión piezorresistivos consisten en una membrana (principalmente de silicio) con galgas extensométricas integradas realizadas con semiconductores que detectan la deformación derivada de la presión aplicada. Estas galgas extensométricas se suelen configurar formando puente de Wheatstone, para reducir la sensibilidad e incrementar la potencia de la salida. Este puente con semiconductores es de un factor de 10 a 100 veces mayor que con resistencias de metal puro. Debido al material utilizado, pueden utilizarse hasta presiones en torno a 1000 bar.
Las galgas extensiométricas metálicas montadas en puente de Wheatstone pueden colocarse en cualquier material mientras las realizadas con semiconductoras están incorporadas como microstructura en la membrana de este modo la deformación se hace de manera directa, pero tienen la desventaja que son muy sensibles a la temperatura y necesitan una compensación individual para cada sensor.
- Los sensores de presión piezorresistivos consisten en una membrana (principalmente de silicio) con galgas extensométricas integradas realizadas con semiconductores que detectan la deformación derivada de la presión aplicada. Estas galgas extensométricas se suelen configurar formando puente de Wheatstone, para reducir la sensibilidad e incrementar la potencia de la salida. Este puente con semiconductores es de un factor de 10 a 100 veces mayor que con resistencias de metal puro. Debido al material utilizado, pueden utilizarse hasta presiones en torno a 1000 bar.
-
Tipos de medidas de presión
Para elegir un sensor de presión, es esencial entender que se consideran 3 tipos de presión, correspondientes a modalidades de sensores diferentes.
Como se ha comentado, la mayoría de las tecnologías de los sensores de presión miden la deformación de una membrana bajo el efecto de la presión ejercida sobre ella, siendo este el valor que se desea conocer. Como la membrana dispone de dos lados, se aplica otra presión sobre el segundo lado, por lo que la deformación medida es el resultado de la diferencia de presión entre los dos lados de la membrana.
Se consideran 3 tipos de presión de referencia (absoluta, relativa y diferencial) y, por lo tanto, tendremos 3 tipos de sensores:
-
-
- Los sensores de presión absoluta miden la presión con respecto a una cámara de referencia sometida al vacío (cercana al vacío). La deformación de la membrana corresponde exactamente a la presión medida. Tiene la ventaja de que no se ven afectados por los cambios en la presión atmosférica y, además los cambios de temperatura influyen en menor medida en su funcionamiento.
- Los sensores de presión relativa (presión manométrica o manómetros) se emplean para medir la presión en relación con la presión atmosférica presente en ese momento. El segundo lado de la membrana está sometido a la presión atmosférica. Su deformación equivale a la diferencia entre la presión medida y la presión ambiente.
- Los sensores de presión relativa normalizada (Manómetros sellados o de referencia constante) son como los sensores de presión relativa que miden la presión con respecto a una presión fija, en lugar de con respecto a la presión atmosférica existente.
Los sensores de presión diferencial determinan la diferencia entre dos presiones y se pueden utilizar para medir caídas de presión, niveles de fluidos y caudales. Técnicamente, la mayoría de los sensores de presión son en realidad sensores de presión diferencial. Por ejemplo, un manómetro es un sensor de presión diferencial con un extremo abierto a la presión ambiente.
-
Cuando la presión que mide un sensor de presión relativa o manómetro es igual a la de la atmósfera, la presión manométrica es igual a cero, de forma que no hay una diferencia de presión entre el sistema analizado y el entorno atmosférico. Cuando se conecta un manómetro al sistema cuya presión se desea medir, miden el exceso de presión respecto a la presión atmosférica. Si la presión en dicho recinto es menor o igual a la atmosférica, señala cero.
Un vacío perfecto correspondería a la presión absoluta cero. Todos los valores de la presión absoluta son positivos.
Las presiones por debajo de la atmosférica reciben el nombre de presiones de vacío. Cuando el sensor de presión mide presiones por debajo de la atmosférica se habla de sensor de presión de vacío o vacuómetro.
Las presiones absoluta, manométrica y de vacío son cantidades positivas y se relacionan entre sí por medio de:
Pman = Pabs – Patm (para presiones superiores a la Patm )
Pvac = Patm – Pabs (para presiones inferiores a la Patm )
donde Pman = Presión manométrica; Pvac = Presión de vacío; Pabs = Presión absoluta; Patm = Presión atmosférica.
Fig: Esquema de relaciones entre la presión absoluta, atmosférica y manométrica →
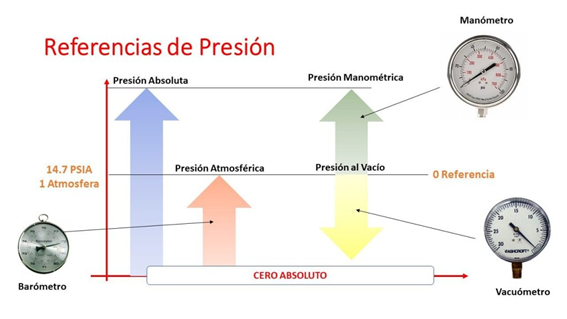
Variables Físicas medidas indirectamente con Presión
Hay variable como el nivel y el caudal que pueden medirse a través de sensores de presión.
-
-
- Medición de nivel con sensores de presión: Sensores de presión hidrostáticos.
- Sensores de presión diferencial: medición de caudal.
-
Como elegir un sensor de presión
Después de conocer si se necesita medir la presión absoluta, relativa o diferencial y de haber elegido una tecnología de sensor, habrá que elegir el modelo correcto de acuerdo con los siguientes criterios:
Características estáticas:
-
-
- En primer lugar, es importante elegir un sensor cuyo rango de medición corresponda al rango de presión que se desea medir, teniendo en cuenta las condiciones normales y las posibles variaciones de presión.
- Por supuesto no hay que olvidar las especificaciones de las características de medida que necesitemos para nuestra aplicación, como cuando se elige cualquier sensor: Precisión, Repetibilidad, histéresis, deriva, etc.
-
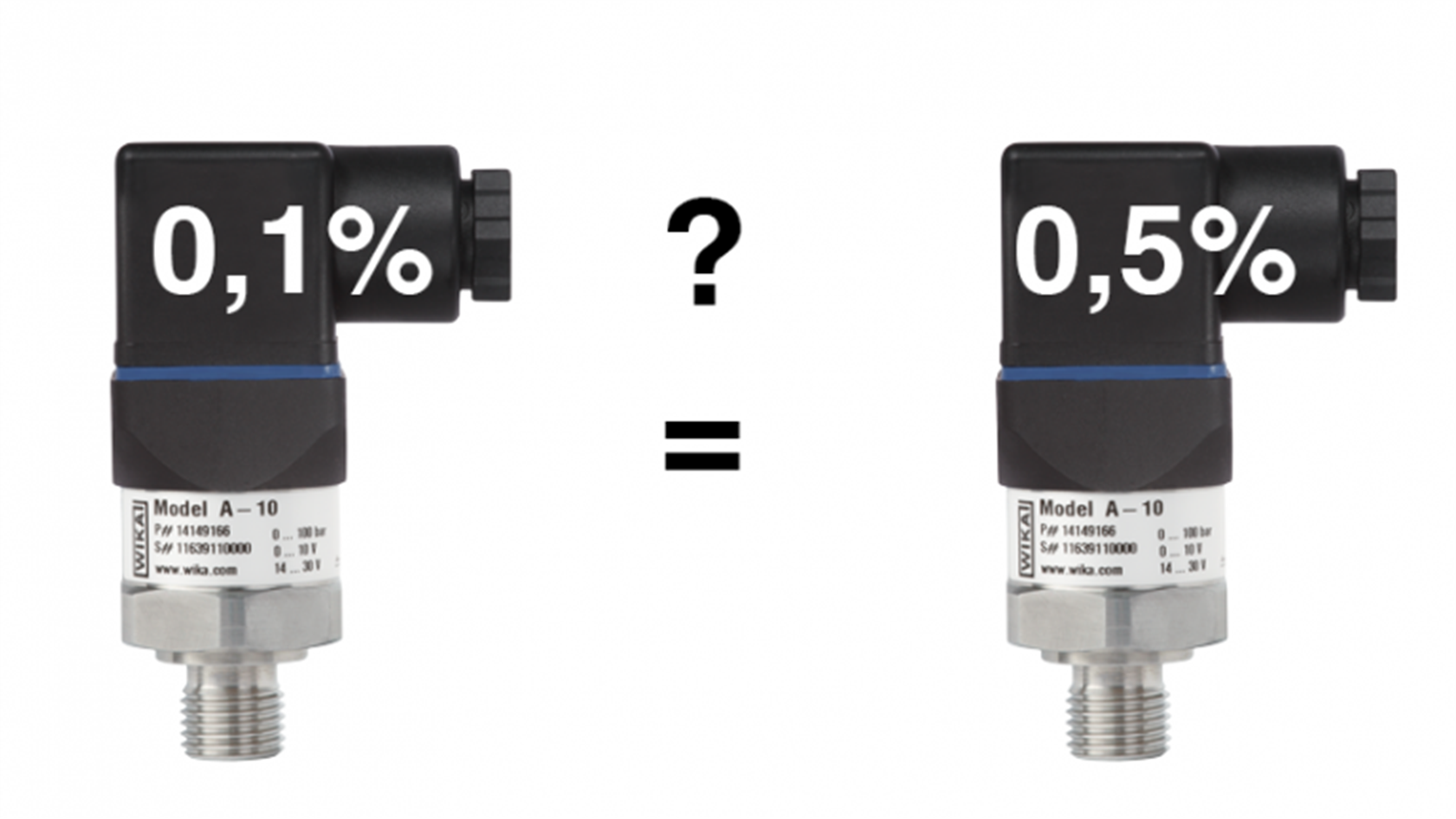
← Fig: La precisión y la baja deriva del sensor influye en su precio. A más preciso más caro. La deriva se puede corregir calibrando el sensor una vez al año. La histéresis es el único parámetro que no podremos corregir
Características ambientales:
-
-
- La temperatura de funcionamiento en nuestras aplicaciones no juega un papel importante. La mayoría de los sensores tienen una gama de funcionamiento de -25 °C a 100 °C.
- Características mecánicas: Grado de protección IP. Grado de protección EX. Grado de protección IK.
-

Características eléctricas:
-
-
- Tensión de alimentación: 5 Vcc, 10-30 Vcc , etc.
- Señal de salida: Al igual que con cualquier otro sensor, se deberá elegir un sensor de presión cuya señal de salida pueda ser recogida por nuestro equipo electrónico: 4-20 mA; 0-10 V; 0-5 V; etc. También nos podemos encontrar sensores con salidas de comunicaciones industriales (Modbus sobre RS-485) o electrónicas (I2C, SPI)
- Consumo (Si va a estar alimentado por un nodo autónomo, es de los parámetros que nos va a fijar el sensor a instalar).
- Protecciones contra sobretensiones y cortocircuitos.
- Conexión eléctrica: 2/3/4 hilos, tipo de conector. Nos vamos a encontrar varios tipos de salida, pero siempre debemos elegir una estandarizada para que el cambio en caso de rotura sea fácil.
-
- Conexión a proceso: El último criterio clave para elegir es la configuración del sensor y cómo se monta en el punto de medición. La mayoría de los sensores son roscados con roscas estandares, lo que permite montarlos fácilmente en una boquilla instalada en tuberías, tanques, etc. También existen sensores equipados con bridas.
Como vemos existen demasiadas variantes a especificar para asegurarnos la óptima adaptación a nuestra aplicación, por eso es interesante elegir marcas que tengan un catálogo amplio con conexiones estandarizadas y que especifiquen bien las características de los sensores.